С тех пор, как в устье реки Вина на атлантическом побережье Франции был торжественно спущен на воду первый деревянный парусник, спроектированный и построенный Бенжамином Бенето по традиционным рыбацким рецептам, прошло уже более 120 лет. А в наши дни, за границей уже третьего века мировой истории, основанная им компания Beneteau — это самая настоящая судостроительная империя, на которую так или иначе приходится равняться прочим производителям парусных и моторных судов.
Воспользовавшись любезным приглашением высшего руководства компании, мы посетили ее производство и наглядно ознакомились с тем, как появляются на свет знаменитые лодки Beneteau.
Традиции и инновации
На заре своего существования компания выпускала в основном деревянные парусники “делового” назначения, выполняя заказы местных рыбаков, которым требовались надежные и вместительные суда, способные выйти в море практически в любую погоду. Лодки Beneteau, основанные на веками проверенных судостроительных решениях, вполне таких заказчиков удовлетворяли.
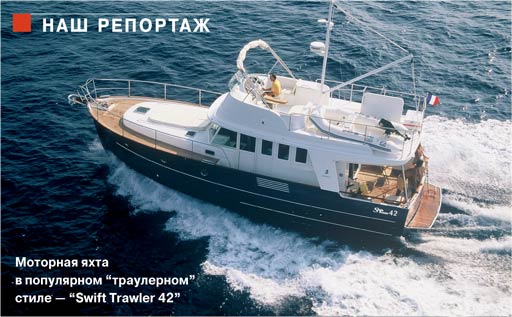
Однако приверженность традициям и несколько настороженное отношение ко всякого рода революционным преобразованиям, исторически характерные для обитателей Вандеи — той области Франции на берегу Атлантического океана, где зародилась компания — никогда не мешали ей идти в ногу с техническим прогрессом. Так, например, первая лодка с мотором, призванным потеснить господствующий парус, сошла со стапелей Beneteau еще в 1912 г.
С особенностью вандейского менталитета связана и курьезная история создания первой стеклопластиковой лодки, на свой страх и риск построенной Beneteau по заказу одного местного рыбака уже в следующем веке, в середине шестидесятых. Узрев вместо привычного дерева незнакомый материал, заказчик категорически отказался платить за “эту дрянь” и со скандалом удалился.
С особенностью вандейского менталитета связана и курьезная история создания первой стеклопластиковой лодки, на свой страх и риск построенной Beneteau по заказу одного местного рыбака уже в следующем веке, в середине шестидесятых. Узрев вместо привычного дерева незнакомый материал, заказчик категорически отказался платить за “эту дрянь” и со скандалом удалился.

Обескураженные экспериментаторы убрали лодку с глаз долой и почти забыли о ней, пока вдруг не появился некий парижский коммерсант, которому требовалась прогулочная яхта. Тот без вопросов забрал пылящийся на задворках верфи пластиковый парусник, соблазненный перспективой получить яхту сразу, не дожидаясь положенных сроков выполнения заказа. Вскоре с его подачи один за другим стали появляться другие столичные любители отдыха на воде, которые в один голос просили такую же лодку.
Вдохновленная успехом, Beneteau представила на Парижской бот-шоу 1965 г. сразу несколько стеклопластиковых моделей, и с тех пор львиная доля судов компании — и прогулочных яхт, и профессиональных рыбацких траулеров — строится исключительно из этого материала.
Масштабы
На сегодняшний день Beneteau представляет собой не просто единичную верфь, а гигантскую промышленно-финансовую группу, владеющую множеством предприятий, причем не только во Франции — с 1986 г. она строит яхты и на территории США. Основным родом деятельности, как и встарь, является серийное производство прогулочных судов, которое осуществляют собственно Beneteau и компания “Jeanneau”, приобретенная ею в 1995 г. На их долю приходится около 80% торгового оборота группы. Строят они в основном парусные яхты — это 79% общего объема выпуска.
Судостроением занимаются и входящие в группу предприятия “CNB” (“Construction Navale Bordeaux”), и “Wauquiez”, которые строят суда профессионального назначения, катамараны и парусные мегаяхты по спецзаказам.
Тесное отношение к яхтенному направлению имеют торговые компании “European Yacht Brokerage” и “SGB Finance” с представительствами по всему миру, работающие на первичном и вторичном рынках парусных и моторных судов. Кроме того, Beneteau строит загородные дома и даже… выпускает автомобили — крошку размером почти с нашу “Оку”, но не требующую водительских прав, поскольку рабочий объем двигателя не превышает 50 см3. С конвейера их сходит ни много ни мало 7000 шт. в год.
На 18 заводах (из которых шесть верфей и две специализированные столярные фабрики строят прогулочные лодки под маркой Beneteau) суммарной площадью 263 479 м2 трудится более 4000 рабочих и служащих. Согласно финансовым отчетам, общий объем продаж предприятий группы в 2002 г. составил более 640 млн. евро, а неуклонно растущая прибыль — почти 62 млн.
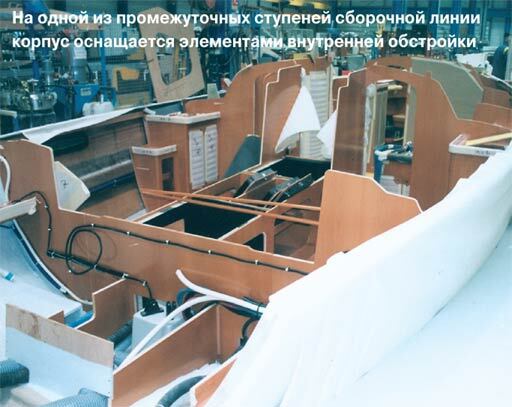
В общем, масштабы поистине космические. Достаточно сказать, что в горячую пору за ворота только двух верфей, которые нам довелось посетить, могут выкатывать в общей сложности по восемь готовых лодок в день — причем не просто лодок, а парусных и моторных яхт более 12 м. длиной! Сейчас под маркой Beneteau выпускается 21 модель парусных лодок (наиболее известные “линии” — “First” и “Oceanis”), и 22 моторных — легкие “Flyer”, спортивные “Ombrine”, крейсерские “Antares”, а также популярные в последние годы мореходные крейсера в “траулерном” стиле.
И еще один показательный факт — по количеству построенных за год парусных яхт длиной от 20 до 57 футов (6 -17 м.) компания занимает первое место в мире.
Централизация и специализация
Каким образом при таких объемах выпуска — даже с учетом многообразия модельного ряда — Beneteau удается предлагать потребителю не “штамповки”, а действительно штучные лодки?
Во-первых, как объяснил нам менеджер по экспорту компании Beneteau Франсуа Родрик, взявший на себя роль нашего гида, действительно, широкий модельный ряд — это лишь видимая часть айсберга. Каждая из 43 парусных и моторных моделей может иметь до десятка модификаций и вариантов исполнения, отличающихся планировкой, деталями отделки и оборудования, силовыми установками, так что лодки одной и той же модели далеко не всегда похожи, как две капли воды.
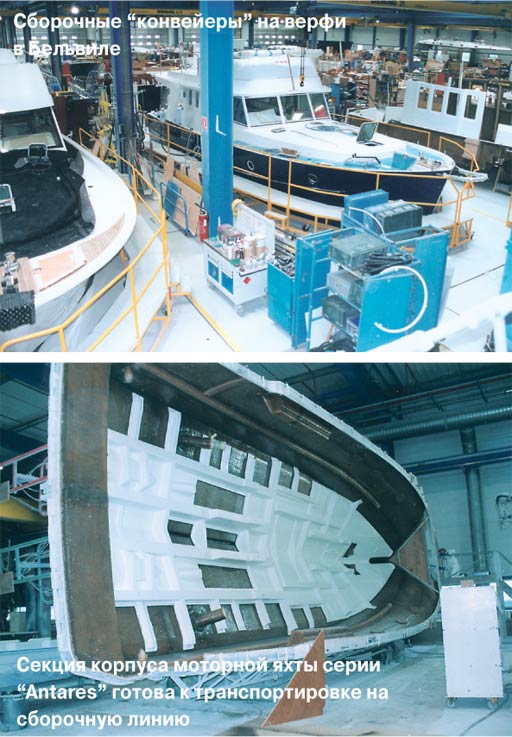
Здесь же приводится перечень и комплектация модулей. “Адрес”, по которому следует передвинуть подготовленный модуль, представляет собой цифровой код, основой которого является серийный номер будущей лодки. Заранее раскроенный и разложенный на полочки в контейнере № 046 армирующий материал-сшивку (стеклорогожу крупного переплетения со стекломатом) на наших глазах откатили к готовой для формования матрице секции корпуса Beneteau 44.7 с точно таким же номером, на которую в соответствии с паспортом был уже нанесен темно-синий гелькоут — пожелание заказчика. Вместе с установкой внутренней секции набора процесс займет два-три дня.
Кстати, по словам Франсуа, эта модель пользуется таким спросом, что предприятие намерено изготовить второй набор матриц, хотя и один при надлежащем уходе способен выдержать несколько сотен формовок. Готовый корпус вместе с палубной секцией, которую формуют под тем же номером в том же цехе, отправится на сборочную линию, куда точно в срок подвезут номерные контейнеры с деревянными панелями внутренней обстройки, дельными вещами и прочими заранее подобранными деталями, поступившими с других участков, а также зарешеченный ящик с двигателем в комплекте со всеми сопутствующими системами — будущий владелец яхты с заводским номером “046” заказал “Yanmar”, а не “Volvo Penta”, и может быть уверен, что путаницы не произойдет.
Конвейер
Сборочные линии на яхтенном производстве — явление крайне редкое, и до сих пор нам доводилось видеть нечто подобное только на “продвинутой” итальянской верфи “Gobbi” (см. № 187). На новом заводе Beneteau в Бельвиле таких линий шесть, а на верфи в Сен-Жиле, которую мы посетили в тот же день (выпускает парусные яхты от 14 м. длиной и катамараны) — целых десять.
Установленный на колесный стапель корпус последовательно проходит пять ступеней, строго по расписанию обрастая оборудованием под руками узких специалистов: на одной устанавливают двигатель со всеми сопутствующими системами, на другой монтируют электрику, на третьей завершают оборудование кают…
На каждой ступени “конвейера” можно увидеть упомянутые модули с номерами — больше всего здесь тележек-пеналов со сверкающими деревянными переборками. Душевые кабины, камбузные блоки, гальюны поставляются сюда в уже собранном виде — с заранее поставленными кранами, раковинами, полочками и даже крючками для полотенец, остается только установить их на место и подсоединить к соответствующим электрическим, водопроводным и фановым системам.
В общем, все здесь направлено на то, чтобы рационально использовать рабочее время и по возможности упростить технологию — скажем, те же лебедки, швартовные утки, вант-путенсы и т.п. монтируются на секцию палубы заранее, до ее стыковки с корпусом, когда ко всем элементам крепежа можно подобраться без проблем.
На каждой “остановке” имеется большой стенд, на котором помимо рабочих чертежей можно найти подробные инструкции, проиллюстрированные фотографиями, и если кто-то из рабочих находит способ выполнить ту или иную операцию проще, быстрей и качественней, то изобретенный им прием вскоре будет в наглядном виде доведен до его коллег на других сборочных линиях.
На ошибках учат и технике безопасности — на одном из стендов мы обнаружили листок с силуэтом руки и красной точкой на нем, обозначающей место травмы (была указана и дата происшествия), а рядом с ним цветную фотографию, демонстрирующую, как правильно надо было держать инструмент. Да и вообще с охраной труда здесь все в порядке — повсюду установлены системы кондиционирования воздуха, снабженные специальными фильтрами, так что запах стирола, характерный для стеклопластикового производства, практически неощутим.
Образующаяся при механической обработке пластика и дерева пыль сразу удаляется пылесосами, шланги которых вмонтированы непосредственно в станки и ручные инструменты. Пять ступеней сборочной линии лодка проходит примерно за неделю; промежутки между ними — два-три дня, за которые специалисты должны полностью завершить свой этап работы.
Становится понятно, откуда берутся кажущиеся невероятными объемы выпуска: Бельвиль выдает 600 лодок в год, а Сен-Жиль — около 1000. При этом не будем забывать, что посетили мы только две верфи Beneteau из шести…
Борьба за качество
Эту знакомую фразу из уст Франсуа мы слышали не единожды — правда, не по-русски. У нашего человека подобное словосочетание способно вызвать в лучшем случае скепсис. Но, как видно, основной вопрос в том, как именно бороться — лозунгами или делом. Главный инструмент штатных борцов за качество на верфях Beneteau — это обыкновенный рулон клейкой ленты ярко-красного или желтого цвета, размеченный на квадратики с порядковыми номерами от единицы и далее.
Заметил брак — отрывай наклейку и лепи ее рядом с обнаруженным недочетом, да не забудь продублировать информацию на отдельном листке со схематичным изображением целой лодки или отдельного узла. Сразу видно и место брака, и его порядковый номер.
С контролерами местного ОТК не забалуешь: иную волосяную царапину на сверкающем корпусе 57-футовой яхты, отмеченную наклейкой, можно разглядеть разве что через лупу, но ее все равно придется заделать — только тогда в соответствующей табличке появится сакраментальное “ОК”. “Кривая качества снижается!” — с довольным видом заметил Франсуа, указывая на график, укрепленный рядом со строящимся “Oceanis 411” с серийным номером “1040”. И впрямь было чему радоваться, ведь высота кривой на графикe напрямую зависит от числа заработанных “штрафных” наклеек. Обнаружилась на графике и горизонтальная прямая черта — норматив, к которому следует стремиться.
По словам нашего гида, еще в прошлом году линия “цели” была на пару пунктов выше — пресловутая борьба за качество неуклонно приносит свои плоды. Окончательное тестирование каждой готовой яхты проводится в огромном испытательном бассейне. На его “берегу” чувствуешь себя, словно на настоящем причале — постукивают на холостых оборотах движки лодок, поплевывая за борт горячей водой, витает запашок сырого дизельного выхлопа… Тут же, как в марине, установлена обычная топливная колонка и на стене висит спасательный круг.
В условиях, приближенных к реальным, можно убедиться не только в отсутствии водотечности корпуса или исправности системы охлаждения двигателя — установки искусственного дождя по краям бассейна готовы обрушить на лодку настоящий тропический ливень, подвергнув проверке на герметичность иллюминаторы, люки, двери и точки крепления внешнего оборудования.
“Столярка”
Наиболее характерная иллюстрация “модульного принципа” производства Beneteau — это две отдельные фабрики, которые изготавливают деревянные детали для всех без исключения верфей компании, включая и американскую. Одну из них мы посетили на второй день визита. Отсюда готовые наборы, включающие абсолютно всю “столярку” — от переборок до откидных столиков — поставляются в пронумерованных контейнерах на сборочные линии.
Дорогие породы дерева доставляются сюда в виде распиленных на толстые доски бревен. Наиболее ответственные деревянные детали, которые и придают лодкам Beneteau яхтенный шик, делают только из “массива” или, если деталь имеет сложную форму, из шпонового ламината (шпон красного дерева или вишни готовят при этом сами). Все такие работы осуществляются вручную, хотя и не без помощи специальных станков и прессов, покрывают готовые детали лаком тоже вручную.
А вот большие переборки и скрытые от глаза деревянные панели делают из обычной водостойкой фанеры, облагороженной дорогим шпоном. При этом лак наносится автоматизированными линиями, снабженными ультрафиолетовыми сушилками (пять минут — и сверкающая заготовка укладывается пневмоприсосками в общий штабель), а вырезают и фрезеруют детали станки с ЧПУ. Точность и ручной работы, и автоматизированной поистине ювелирная — подгонка по месту на верфи не понадобится.
В соседнем со столярной фабрикой здании располагается также дизайн-бюро Beneteau, в котором под руководством двух главных конструкторов — “парусного” и “моторного” — трудится около 60 специалистов. Кроме того, компания нередко прибегает к услугам сторонних разработчиков — таких, например, как всемирно известные конструкторские компании “Finot” или “Farr”.
На заключительной встрече в центральном офисе, которую почтила своим присутствием президент компании Аннет Ру, зашел разговор о перспективах Beneteau в России. Честно говоря, вопреки обычной практике пришлось больше отвечать на вопросы, нежели их задавать. Однако было понятно: любезные хозяева в курсе того, что российский ботинг переживает эпоху ренессанса, и поэтому смотрят в будущее с оптимизмом. “Наверняка и у вас в России найдется немало ценителей хороших лодок, к которым мы относим и свою продукцию,” — заключила г-жа президент, внучка знаменитого Бенжамина Бенето.
Автор: Артем Лисочкин
Источник: katera.ru